How to create a fully streamlined warehouse
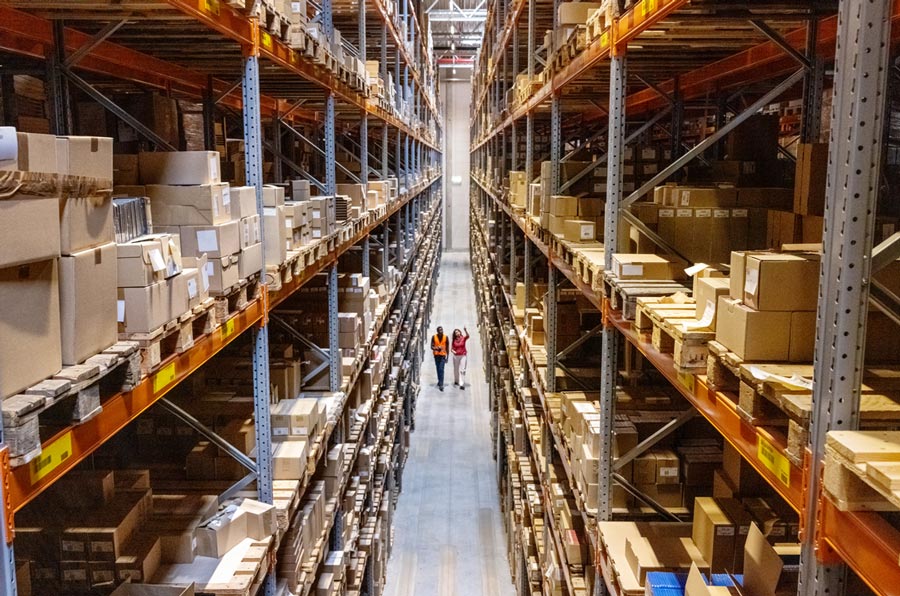
With customers’ expectations continuing to rise, the quality of service becomes increasingly important which is underpinned by the efficiency of your operations and internal processes.
In this blog, we will explore with the expertise of our solution partners Gamma Solutions and TIG Freight, how you can implement the right physical tools and software to further streamline your warehouse and supply chain processes.
The right tools
Let’s start with your physical warehouse environment and the hardware used for packing and picking.
With so many equipment and technology options available to boost warehouse efficiency and productivity, it can be challenging to determine which solutions best suit your operations. Gamma Solutions has broken down the key categories to help clarify your choices.
Types of equipment
Traditional gun-style devices
These pistol-grip devices remain one of the most common tools in the warehouse. Easy to use and often holstered or mounted to forklifts, they feature a hard keyboard and trigger-style scanning.
If your business is using Pronto Xi 760 or earlier, these devices are a perfect match. However, for newer versions such as Pronto Xi 770 or 780, a full touchscreen device is typically the better fit.
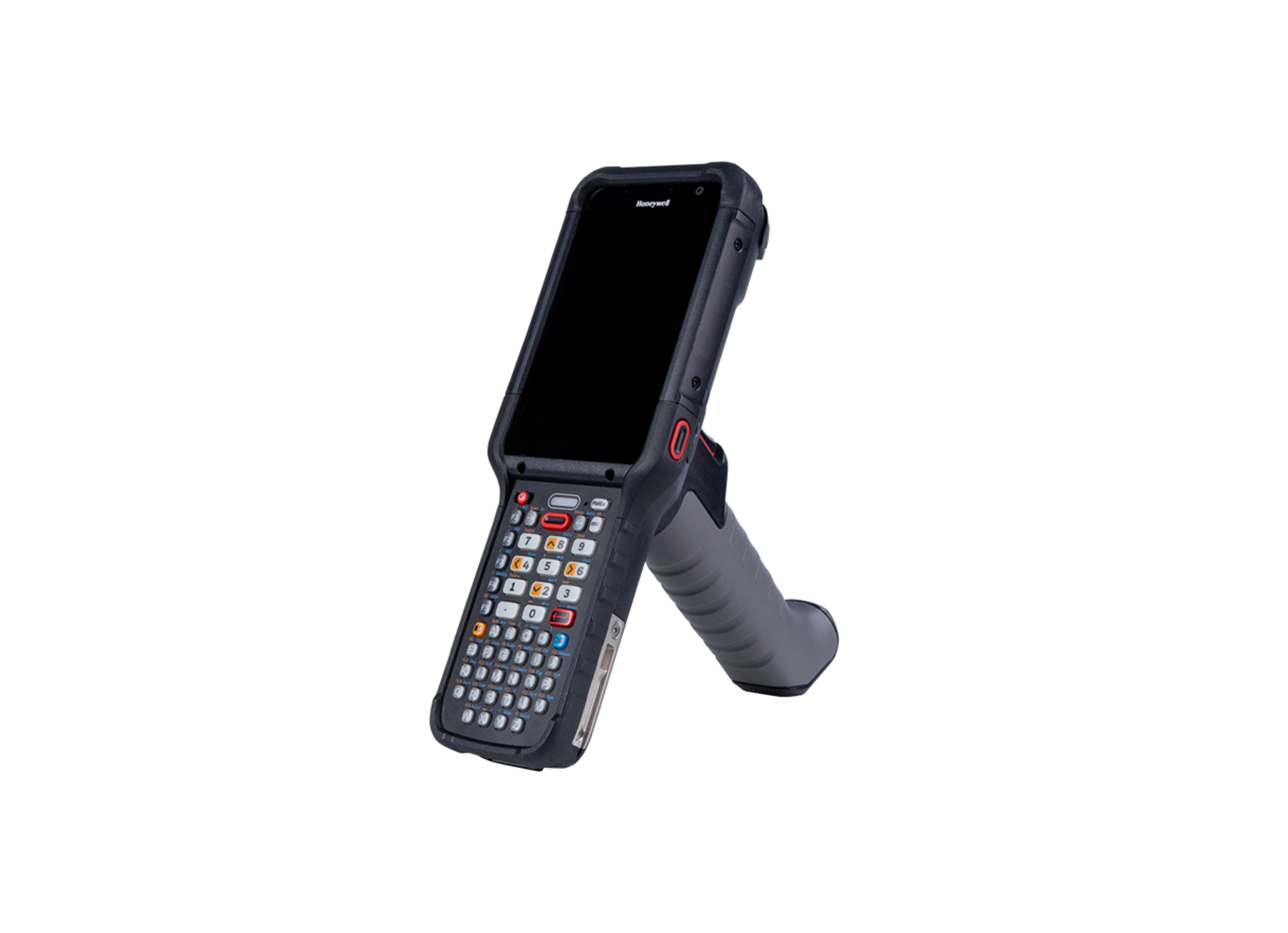
Gun-style scanners are also ideal in environments where gloves are required, like cold storage or when handling bulky goods, making tactile key input more reliable than a touchscreen.
They are available in various scanning ranges:
- Standard Range (30 – 40cm): Ideal for close-range picking.
- Medium/Flex Range (2 – 3m): Perfect when scanning from forklifts.
- Extended Range (7 – 8m): Useful during stocktakes or scanning high-rack pallets from ground level.
Specialised variants:
- Hazardous Location Models: These non-incendive devices are designed for environments with explosive gases. Their rugged construction prevents sparks from dropped batteries and includes protective features for safety.
- Cold Storage Models: Engineered for use in sub-zero environments. These devices feature special batteries and plastics that remain durable in cold conditions, along with heated screens and lenses to prevent fogging or moisture build-up.
Wearable devices
Wearable devices such as arm-mounted terminals or ring scanners free up your hands and allow workers to move and scan inventory without having to constantly pick up and put down a handheld device.
These are especially useful when working with large or heavy inventory that requires both hands to lift. While earlier versions had small displays, the latest models now include keyboards placed below the screen without sacrificing visibility or functionality.
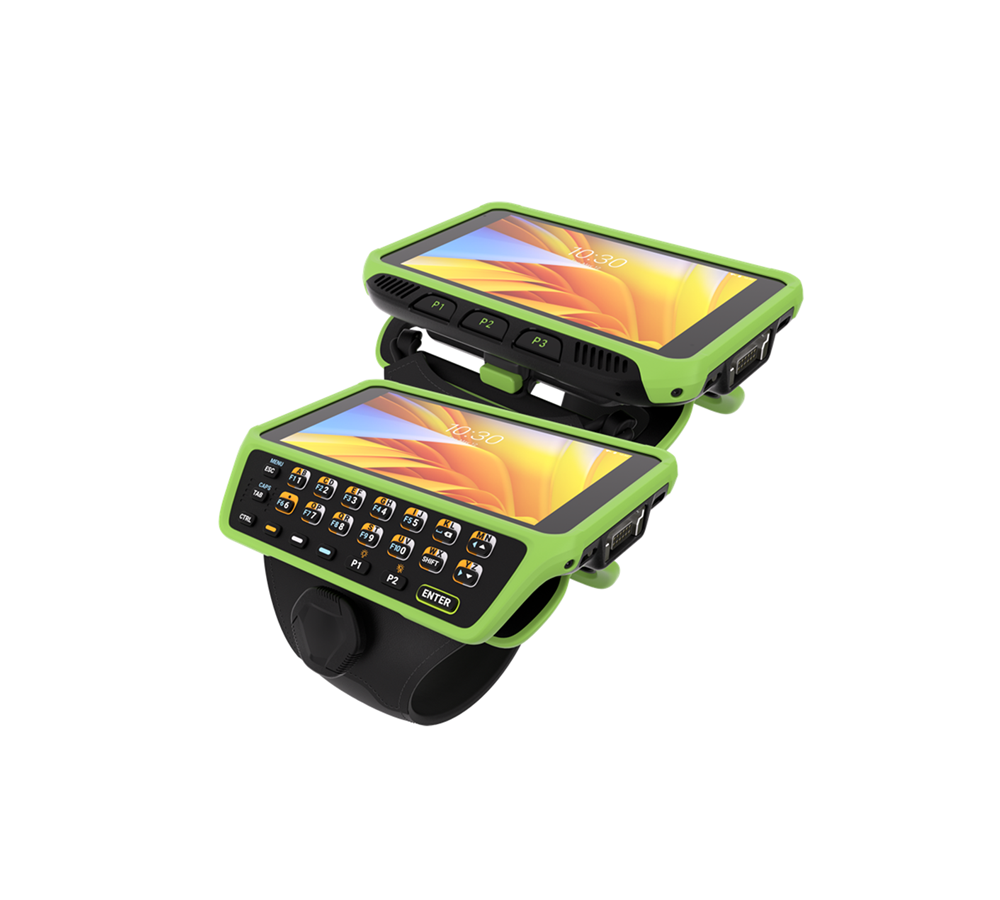
Mobile phone-style devices
Modern touchscreen-based mobile computers now rival traditional scanners in durability, battery life, and scanning range. With increased ruggedness (surviving 2.4-metre drops to concrete), 5G connectivity, and improved affordability, they’ve become a viable option for Warehouse Management Systems (WMS) and day-to-day operations.
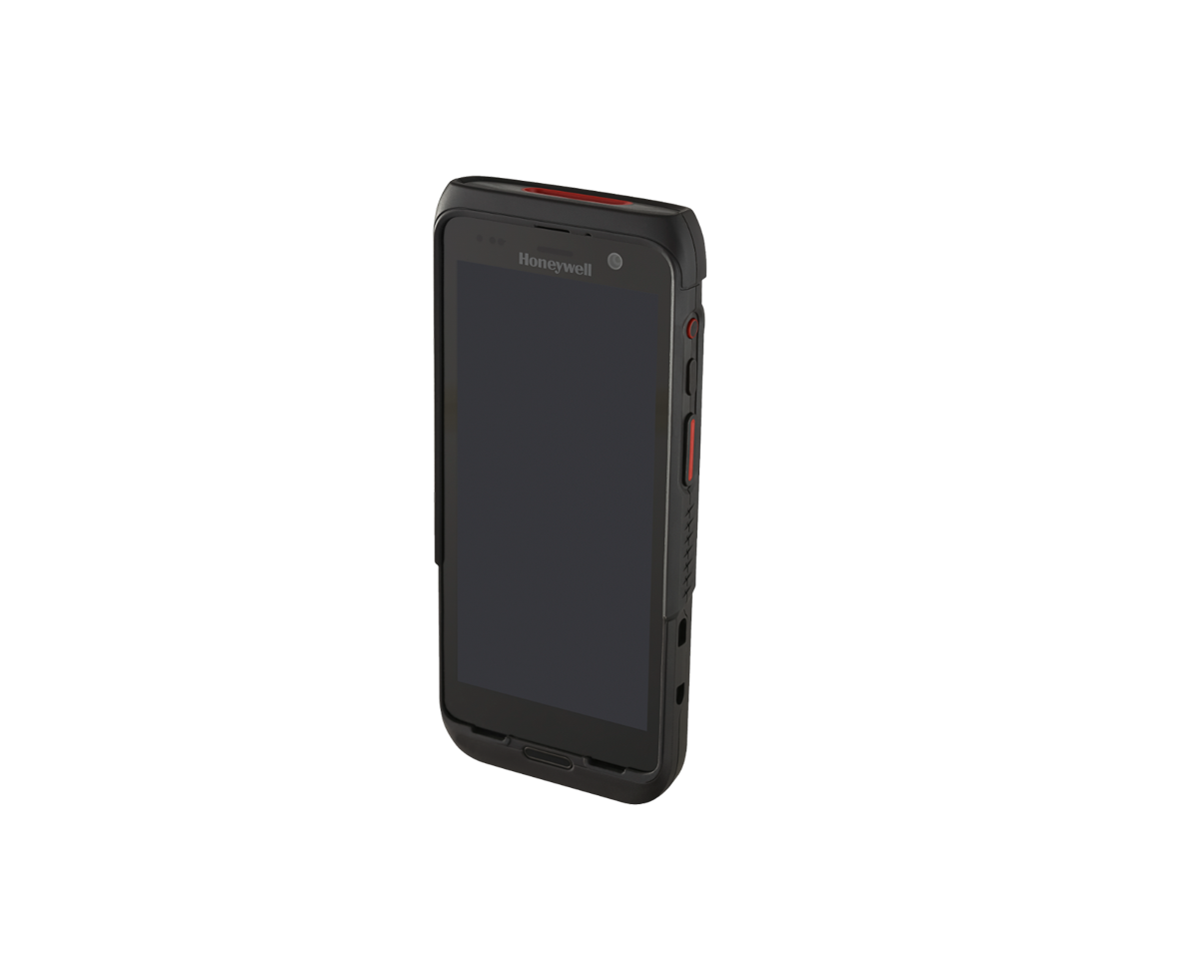
Mobile printers
Portable label printers are a cost-effective solution that many companies under utilise. By allowing workers to print labels on demand either clipped to a belt or mounted on a forklift. There’s no need to walk back and forth to a central printer. This saves time and reduces the risk of incorrect labelling.
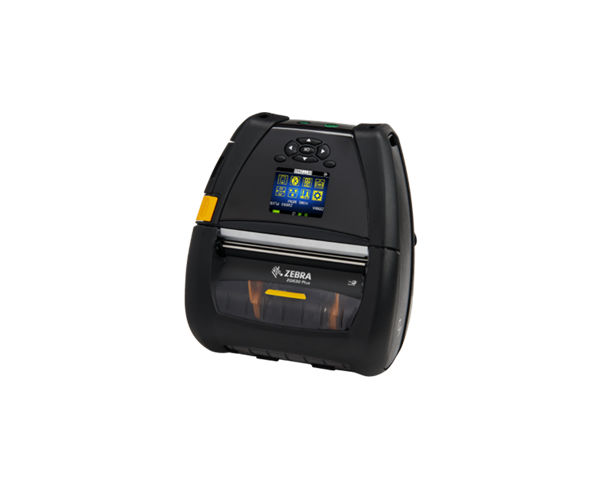
Printers with label verifiers
As printer heads wear down or get dirty, they may produce unreadable labels. This can lead to carrier surcharges or rejected pallets from customers.
A printer with a built-in verifier scans the barcode as it prints. If the barcode is unreadable, the printer marks it as void and automatically reprints a new label minimising costly errors.
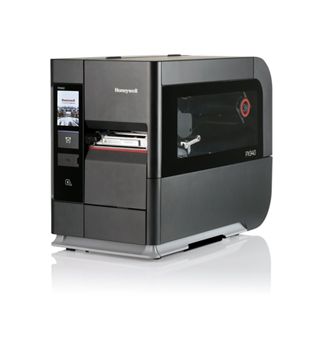
Try before you buy
Regardless of the device or printer, it’s important to test it in your real-world environment. Gamma Solutions supports this process by providing test units for trial typically assigning them to experienced pickers for feedback to ensure the solution is right for your workflow.
The Right Software
Once you have the correct hardware in place, the next step is ensuring you’re supported by the right backend solution and software. We’ve partnered with TIG Freight, a leading freight management and shipping platform with a network of over 200 freight partners across Australia, New Zealand, and internationally.
Pronto Xi ERP x TIG Integration
Our solution, Pronto Xi Supply Chain, delivers end-to-end visibility — from distribution planning and stock forecasting to complete warehouse management.
With a single view of orders, shipments, and inventory, your team can respond more agilely to disruptions while leveraging data-driven insights to maximise profitability.
Through the seamless integration between Pronto Xi and TIG Freight, freight management data is automatically reported and reflected in your core ERP — your single source of truth.
The integration enables freight to be dispatched through three core channels: Sales Order Dispatch, Scan Pack, and RF (Radio Frequency) workflows.
From a data perspective, one of the most valuable benefits of this integration is synchronised freight data, allowing detailed reporting that was previously difficult or time-consuming. This includes shipping costs, consignment numbers, and freight charges linked to each sales order. TIG also supports tracking and proof of delivery within Pronto Xi, giving you complete visibility and enabling deep insights into true freight costs and carrier performance.
Freight Management Partner vs. Direct Carrier
Freight rates typically increase each year. To stay competitive and offset those increases, it’s essential to regularly review your freight providers. If you haven’t assessed your freight partners in the past 12–24 months, now is the time.
Relying solely on a direct carrier can lock your business into a single provider — increasing your exposure to rate hikes, service reductions, or even business closure or acquisition.
With a freight management partner like TIG, you benefit from:
- A single consolidated freight invoice
- One point of contact for all freight-related enquiries
- Ongoing optimisation of your carrier mix and pricing structures
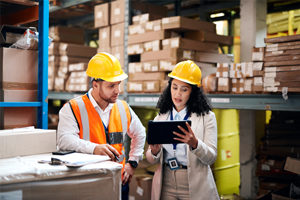
TIG’s flexible approach means you can easily switch carriers as needed — with minimal disruption to your operations. They also offer a free freight health check, making it worthwhile to review your current setup if it’s been some time since your last evaluation.
Freight Management Options with TIG
TIG Freight offers three flexible freight solutions tailored to different business needs:
- Managed Freight Solution:
TIG manages the carrier accounts on your behalf. You receive a consolidated invoice and full support, including a dedicated freight investigator, customer service team, and account manager. This removes the complexity of managing daily freight operations. There are no additional costs for setup or integration. - Platform-Only Solution:
You retain your existing relationships with carriers, while TIG provides the platform and integration with Pronto Xi. Note that setup and management fees apply for this option. - Hybrid Solution:
A combination of your existing carriers and TIG-managed carriers. This flexible approach includes a small setup and integration fee.
Streamline Your Freight Operations
By combining the right hardware, tools, and software, you can streamline your business operations and gain the data insights you need to drive continuous growth. Gamma Solutions & TIG Freight, integrated with Pronto Xi, ensures you’re equipped for smarter freight management and operational success.
To learn more book a one-on-one demo with either Gamma Solutions or TIG Freight.
Let's stay connected
Be the first to receive our resources, including news about your industry.